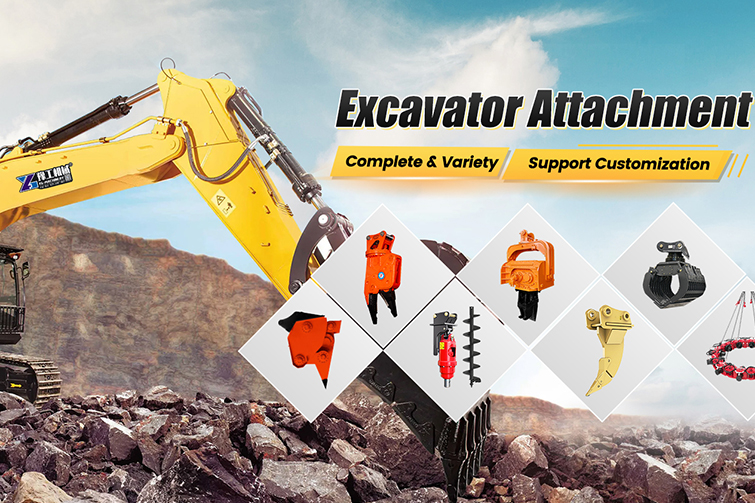
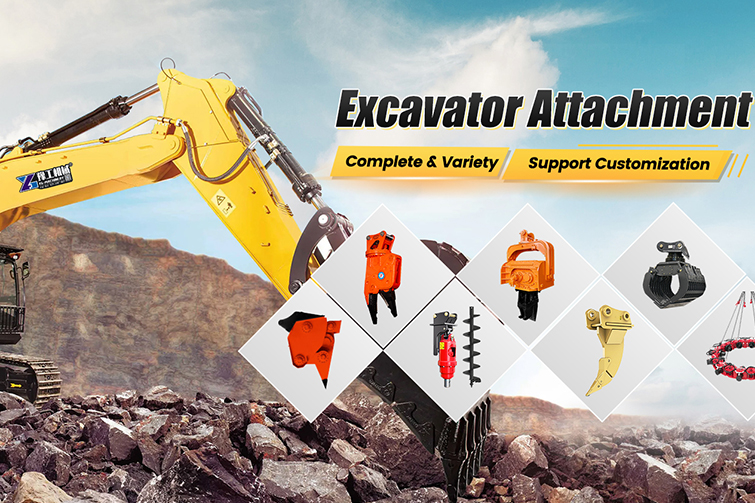
How to Choose an Excavator Grapple Attachment
Excavator grapple attachments, or “grabs,” are essential tools for handling a variety of materials, from rocks and logs to scrap metal and debris. Selecting the right grapple for your excavator can significantly improve job efficiency, safety, and versatility. Here’s a guide to help you choose the best excavator grapple for your needs, covering factors such as grapple type, compatibility, materials, and specific application requirements.
1. Identify the Application Needs
- Material Type: The primary consideration is the type of material the grapple will be handling. For example, timber grapples are designed specifically for logs, while demolition grapples can handle a mix of concrete, steel, and other construction debris. Scrap grapples, on the other hand, are built to manage dense, irregular materials like metal and waste.
- Work Environment: Grapples are often designed for specific environments. Forestry grapples, for instance, are optimized for use in rugged outdoor environments, while lighter-duty grapples may be suitable for general construction sites.
2. Choose the Right Grapple Type
- Rotating vs. Fixed Grapples: Rotating grapples provide greater flexibility, as they allow the operator to rotate the grab without repositioning the excavator. This is useful in tight spaces or when handling irregularly shaped materials. Fixed grapples are generally more affordable and can still be highly effective for straightforward lifting and loading tasks.
- Single-Arm vs. Double-Arm: Double-arm grapples typically offer stronger grip and stability, making them ideal for handling large and heavy loads. Single-arm grapples, while lighter, can still be effective in handling smaller or more uniform materials.
3. Check Compatibility with Your Excavator
- Size and Weight: The grapple’s size and weight must be compatible with your excavator to avoid overloading and ensure safety. Typically, each grapple model will specify compatible excavator tonnage ranges. A grapple that is too large or heavy for your machine can reduce lifting capacity and strain the excavator’s hydraulics.
- Hydraulic Requirements: Some grapples require specific hydraulic flows and pressures to function effectively. Make sure your excavator’s hydraulic system meets the grapple's requirements, particularly for rotating models, which may need additional hydraulic circuits.
4. Evaluate Build Quality and Materials
- Steel Quality: Look for high-strength, wear-resistant steel, as grapples undergo significant stress during operation. Quality steel, such as Hardox or similar grades, extends the grapple’s life and increases durability.
- Wear Parts: Certain grapple types come with replaceable wear parts, such as teeth or edges, which can save on maintenance costs in the long run. If your work involves highly abrasive materials, this feature can be particularly valuable.
5. Consider Safety Features
- Safety Lock and Load-Holding Valves: Many high-quality grapples come with load-holding valves and safety locks, ensuring that the grapple maintains its grip even if hydraulic pressure drops. This is crucial for preventing accidental drops, especially when working with heavy or hazardous materials.
- Overload Protection: Some grapples have overload protection to prevent damage from excessive loads. This feature can prolong the life of both the grapple and the excavator by preventing overexertion of the hydraulic system.
6. Look for Additional Features
- 360-Degree Rotation: If you require versatile material handling, 360-degree rotation can be beneficial, allowing you to grip materials from any angle without repositioning.
- Multi-Purpose Jaws: Some grapples come with interchangeable jaws or multi-purpose jaws, making it possible to use the same grapple for different materials, such as rocks, logs, and scrap metal. This adaptability can increase productivity and reduce costs.
- Automatic Lubrication: Some advanced grapples have automatic lubrication systems to keep joints and moving parts in optimal condition, reducing the need for manual maintenance.
7. Budget and Maintenance Costs
- Initial Investment: Higher-quality grapples tend to have a higher initial cost but often come with better durability and performance, reducing long-term expenses. Balancing upfront costs with expected job efficiency can help you make a cost-effective decision.
- Maintenance and Parts Availability: Choose a brand or model with accessible spare parts and reliable after-sales support. This can reduce downtime due to maintenance and repairs. Also, consider whether the grapple requires frequent maintenance, as regular downtime can impact overall productivity.
Conclusion
Selecting the right excavator grapple attachment involves evaluating factors like grapple type, compatibility, material durability, and additional features tailored to your specific application. By focusing on the needs of your job site and the capabilities of your excavator, you can find a high-quality grapple that maximizes efficiency, safety, and durability. A well-chosen grapple will not only make your excavator more versatile but also enhance overall productivity, saving both time and operational costs in the long run.